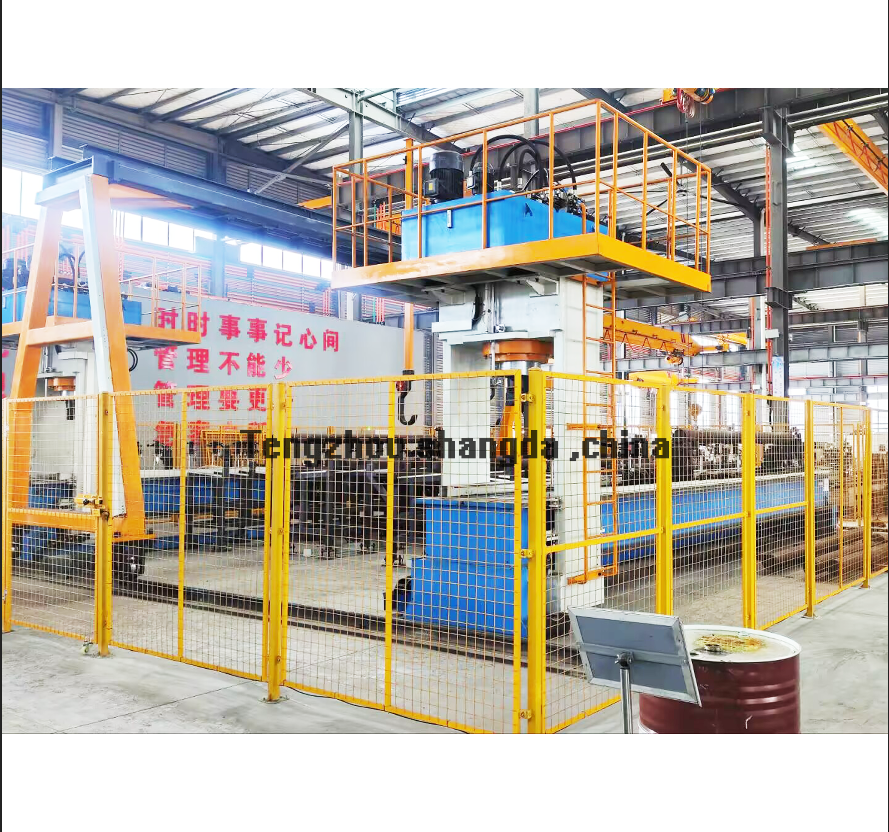
Automatic Straightening Machine for Tube
Discover how AI-powered fully automatic tube straightening machines achieve ±0.005mm precision and 300 tubes/hour throughput
slashing production costs for metalworking industries.
The Precision Problem in Metalworking
In industries where a hair’s width (0.01mm) can mean the difference between profit and loss, traditional tube straightening methods struggle with consistency.
Manual adjustments, material springback, and tool wear cause deviations that lead to scrap rates as high as 15%—a costly bottleneck for manufacturers of hydraulic cylinders, automotive components, and aerospace tubing.
How AI-Driven Straightening Machines Achieve Unmatched Accuracy
Neural Networks in Action
AI algorithms analyze real-time data from laser scanners and pressure sensors, predicting material behavior 50x faster than human operators.
Example: A bent stainless steel tube (Ø50mm) is scanned, and the system calculates 12 adjustment points in <0.8 seconds.
Self-Learning Compensation
Machines automatically adapt to variables like temperature fluctuations and alloy hardness, maintaining ±0.005mm tolerance even during 24/7 operation.
Case Study: A German auto parts supplier reduced rework costs by 63% after switching to AI straightening.
Hyper-Speed Throughput
Robotic arms with vision-guided loading achieve 300 tubes/hour—3x faster than semi-automatic systems.
Key Metric: 98% uptime with predictive maintenance alerts sent 72 hours before potential failures.